The Requirements
To meet the basic qualification for this position you must be legally authorized to work permanently in the United States for any employer without requiring a Visa transfer or Visa sponsorship. To be a strong fit for the Production Manager opportunity, you will have:- A bachelor's degree in Engineering (Mechanical, Electrical, Chemical or Industrial); Continuous Improvement certification is a plus. Quick question for you - click here
- 5-8+ years of experience in a manufacturing environment, including 2-5 years as a production manager. Quick question for you - click here
- Strong Lean manufacturing, continuous improvement background, including 5S, Kaizen, action plans, 5 Whys -- root cause analysis, etc.
- Knowledge of material, production processes, quality control, costs incurred, techniques for maximizing effective manufacture and distribution of goods.
- Knowledge of OSHA health and safety requirements with a strict commitment to safety.
- Technical general knowledge of machines and tools, such as PLC driven, palletizing and stretch wrapping equipment
- Technical and mechanical skill; the ability to troubleshoot.
- A history of meeting goals and delivering results.
- Inventory process, scan guns, lot and location control experience.
- Strategic and tactical planning skills with the ability to coordinate people and allocate resources.
- Strong computer skills including MS Office Suite programs (i.e. basic Excel, Word and Outlook skills) and ERP experience, SAP or JD Edwards is highly preferred.
- A valid driver's license.
- A dynamic team leadership style including:
- A positive attitude.
- Excellent interpersonal and communication skills.
- High integrity.
- Excellent influencing skills and proven success as a change manager.
- Proven ability to coach and develop a strong team of leaders.
- Ability to motivate others, keeping the morale high while also holding each team member accountable for their responsibilities.
- Outstanding documentation skills.
The Role
Role OverviewReporting to the Plant Manager, as Production Manager, you will manage three direct reports -- Production Supervisors -- each responsible for a first, second or third shift production team of approximately 8 members. The supervisor and his/her team are tasked with delivering desired outcomes for a broad array of production, human capital, and process improvement initiatives, but primarily have focused on three key areas:
- Safety - lockout/tagout and other procedures
- Quality - control plan, proactively working with Quality Control, etc.
- Productivity - working within allowed divinations, line documentation; team communication, etc.
Role Details
Daily, you will communicate with the production supervisors to understand any issues and/or challenges they may have. You'll have a kick-off meeting and then your team will take over and run the line. Typically, five team members are on the main line with three on the cell for packaging the product.
Supervisors will be tasked with ensuring the team keeps up with production by managing work orders, coaching, completing documentation and more. You'll manage at a higher level, prioritizing and implementing production improvements, improving processes, looking at efficiency to cost -- for example, scrap, etc.
More specifically, directly or through your team, you will:
- Set the standard work procedures and hold people accountable for meeting those standards through change management (breaking habits and changing hearts and minds)
- Enforce and ensure that all safety and environmental standards are met according to local, state and federal requirements, delivering zero accidents and injuries.
- Apply continuous improvement tools to obtain operational excellence in quality, cost, and efficiency. Quick question for you - click here
- Lead all labor-force activities on the production floor and establish Standard Operating Procedures (SOPs) for daily processes.
- Plan and execute work schedules, assignments and sequences to meet daily production goals by creating a team environment and eliminating waste.
- Collect, analyze and maintain operations data such as operating rates, equipment capacity, talent efficiency, and cost records to ensure on-time and accurate deliverables.
- Observe and monitor key production indicators to ensure operators conform to the production and processing standards.
- Perform quality checks, including but not limited to packaging, product handling, and delivery service metrics.
- Reduce inventory levels by creating an organized workspace where supplies and inventory are easily accessible;
- Operate equipment as required such as forklifts, mixers, pumps, valves, hand and power tools.
- Oversee maintenance, repairs, and housekeeping of building and all the equipment.
- Conduct new employee training and monitor performance on an ongoing basis with a focus on accountability, engagement, and communication.
- Confer with management to resolve problems, complaints and provide solutions to conflict management.

Note: this description is intended to give you a general overview of the position and is not an exhaustive listing of duties and responsibilities.
More Good Reasons
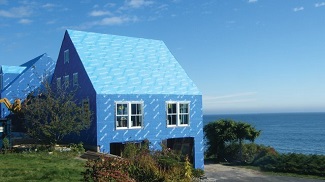
Career options
We’re always on the lookout for talented people with the potential to grow. Right now is a great time to join, as we are in expansion mode, preparing to acquire new companies and expand our footprint. Not only will you support our business plan through your efforts, but you will also spotlight your talent and demonstrate your runway for advancement. Some opportunities may require relocation.
Competitive compensation & benefits
In addition to a competitive salary, you will earn a comprehensive benefits package. As a full-time employee, you will be eligible for benefits including medical, dental, and vision insurance options; company-paid life and disability insurance; a 401(k) retirement plan with matching and independent company contributions; paid holidays, vacation and sick time, and an Employee Assistance Program.
Growing industry leader
Henry® is an industry leader in multiple markets, holding a #1 or #2 position in many of the markets we serve. Our innovative, industry-leading products improve the livability and
Privately owned business
We believe being privately owned is a competitive advantage. Ours is a people-centric culture of entrepreneurship, change, continuous improvement and rewards.
Pictured: Henry Company offers solutions for residential and commercial buildings.
Keys to Success
To excel in this role you will have the interpersonal and leadership skills to supervise and coach diverse personalities and ensure team success. On the whole, you should use a collaborative and motivating approach, but at times you will also need to be assertive. While a heavy-handed leadership approach won't work well with this team, likewise, serving as a team "pal" won't work either. You'll need to earn credibility, bring professionalism and an upbeat attitude to keep the team motivated and productive.Your CI skills will be essential and you take a proactive approach about identifying opportunities to improve processes and cut costs. You will leverage the full extent of your technical skills, be quality-driven, bring an investigative approach, and promote a continuous improvement mindset. When changes are implemented, you will ensure that people are executing correctly and that the change is sustained.
In addition, in order to be an outstanding Production Manager, you will:
- Work effectively with multiple levels and titles in Garland and across the Henry organization.
- Bring a strong sense of urgency to our fast-paced, high volume environment.
- Pay close attention to details while also grasping the big picture and how the details fit into it.
- Manage multiple activities and priorities effectively.
- Remain flexible and adaptable as priorities change.
- Work to remove roadblocks impacting production.